AI in business
Computer Vision in Manufacturing: The 4th Industrial Revolution
Mar 16, 2022
In our latest blog post, we go over seven of the most exciting and disruptive applications of Computer Vision in the industry of retail. Now, let's take a step back and explore what Computer Vision has to offer in Manufacturing.
We cannot do this outside the context of the Fourth Industrial Revolution (4IR), also known as 'Industry 4.0', which is reshaping the manufacturing industry with the incorporation of AI for more efficient processes. By 2025, the technologies behind this revolution are expected to contribute up to $3.7 trillion in value, McKinsey reports.
In 2020, a survey reported revenue increases as well as cost decreases for companies that adopted AI in at least one function. A non-exhaustive list of AI use cases in manufacturing and logistics included yield, energy, and throughput optimization, predictive maintenance, logistics-network optimization, inventory, and parts optimization.
Who are the manufacturing leaders in the 4IR?
In 2018, The World Economic Forum launched the Global Lighthouse Network. This ongoing research project brings together the pioneer companies leading manufacturing innovation. These companies are the frontrunners in adopting 4IR technologies, resetting industry benchmarks, and moving away from the traditional manual manufacturing concept towards a smart and advanced manufacturing model.
The main objective of applying a wide array of technologies (like computer vision) in the manufacturing industry is the optimization of productivity and other key performance metrics. Regardless of the industry, this can be achieved by transforming manufacturing processes through digitalization and automation.
Industry leaders report the positive results of early adoption of 4IR technologies across many manufacturing metrics. Among them, the ones that stand out are:
Increment in overall equipment effectiveness
Deviation drop
Cost of scrap diminution
Cut back in human resources for inspection and validation
Less unexpected breakdowns
Decrement in defects per million
Workforce productivity raise
Decrement in customer complaints
Increment in units produced per hour
Extension of lifespan of equipment
Labor efficiency boost
Production time gain
Cost of goods sold reduction
Improvement of asset utilization
Logistics cost cutback
Rework cost decrement
Performance growth
The lighthouses of manufacturing: what powers them?
These ‘Lighthouses’ come from the most diverse backgrounds in manufacturing. Still, they all focus on the same thing: making the most out of available technology to improve quality of performance without sacrificing efficiency, ultimately driving revenue.
The highlights of these innovations lie in the application of computer vision-powered inspection, predictive maintenance, AI-enabled quality management system automation, 3D printing and big data analytics, real-time machining quality control, among many others.
Computer vision as a part of the revolution
Manufacturing Lighthouses are exploiting AI to continue thriving in an industry that is still very human-dependent. Like in retail, the human factor involves a cost due to the nature of the work: how difficult it is to pay attention to multiple variables simultaneously, the lack of accuracy, and in this particular industry, the added cost of physical safety on the job.
Additionally, the pandemic has exposed the need for the human factor in manufacturing: the knowledge that comes with years on the job, which makes humans difficult to replace, and the vulnerability companies face in a context where the worker's presence may be interrupted.
The solutions AI and Computer Vision brings to the table work towards overcoming these limitations and better use of existing human capital.
Computer Vision is a solution for improving the capabilities of manufacturers and eliminating weaknesses across industries. This is why the industry leaders trust this technology to keep scaling up innovation.
Building and applying customized computer vision algorithms in manufacturing is the road to achieving target KPIs through actionable visual data from daily operations.
Four areas where computer vision has the most significant impact
Computer Vision has limitless potential, but four particular aspects of a manufacturer's operations can benefit greatly from using this technology.
Quality assurance
As one of the industry’s top performance metrics, quality is always the main focus of improvement. It’s transversal to all processes and lines of business. When overlooked, the costs far outweigh the investment in a quality management system. For manufacturers, these costs could arise from rework time, repairs, recalls, scrap, inspection costs, warranty charges, and late delivery penalties.
To avoid the costs of poor quality, manufacturers must invest in good, reliable tools to ensure the quality of the whole pipeline: from raw materials up to the delivery of the final product. Here, Computer Vision plays a vital role in the making of a product when inspecting its components and the final version. With defect detection by automated inspection, two main goals are achieved:
No subtle defect goes unnoticed
Automation allows for consistency of criteria regardless of the workload

With a quality control system composed of Computer Vision-powered cameras, errors can be identified and classified. Products may go on a different route depending on the defect before going on to the next production stage. This classification also allows detecting weak points of the production process and improving where needed.
Catching faulty products and defective raw materials early in the production line reduces the chances of recalls. This way, manufacturers avoid the additional costs of transportation of the faulty goods, not to mention the inconveniences for the sales pipeline and the effects on customer loyalty.
As cameras recognize specific patterns when inspecting an item, image processing algorithms can detect what constitutes an error and send an alert accordingly. What’s more, they can also catch trends when parameters fall within an established range but lie at upper/lower limits, which may indicate a potential problem if not addressed.
But faulty products are not the only concern of automated quality control systems. Nowadays, the appearance of the final product is also essential for downstream sales processes and the overall reputation of the manufacturer.
At this stage, manufacturers must ensure that packaging standards are met. This involves barcodes, texts, and making sure that labels and compliance marks are visible and placed appropriately. The role of Computer Vision in Manufacturing for these processes is clear: detecting, identifying, and diverting items that do not meet the standards before leaving the manufacturing premises, saving the manufacturer of considerable costs.
Lastly, consistent and strict quality controls also allow manufacturers to obtain quality and good manufacturing certificates that indicate compliance with a set of manufacturing standards. These certificates are essential for commercializing certain goods in highly regulated markets, such as drugs or medical devices.
Production
Designing and customizing Computer Vision algorithms to optimize an otherwise manual human task involves process and production engineers and Computer Vision experts. They work as a team with clear, quantifiable goals and know how they affect the manufacturer's KPIs.
Computer vision algorithms can perform predictive maintenance of manufacturing equipment and fleet assets. The model monitors visual indicators such as rustiness, shape, or surface to identify errors or deviations from standards. The model is trained to be as accurate as desired to detect known or unknown indicators of wear and deterioration that could lead to further breakdown of valuable equipment.

Predictive maintenance allows manufacturers to carry out machinery performance analysis. This crucial input prevents workers from changing machinery components that don't need to be changed. This way, manufacturers don't have to face the costs of disassembling equipment to change a part that could run for six more months. As a result, predictive maintenance reduces the annual maintenance cost and gives insight into the lifespan of the components.
Once an error is identified, the system issues a remote warning or displays an alert in the corresponding andon board so that workers have the opportunity to decide what action to take depending on the type and severity of the error in a timely manner.
As a result, the manufacturer avoids losses in equipment and extends the life span of their assets. Most importantly, if production must come to a halt, they can make the corresponding arrangements not to affect the following processes and reduce unplanned downtime.
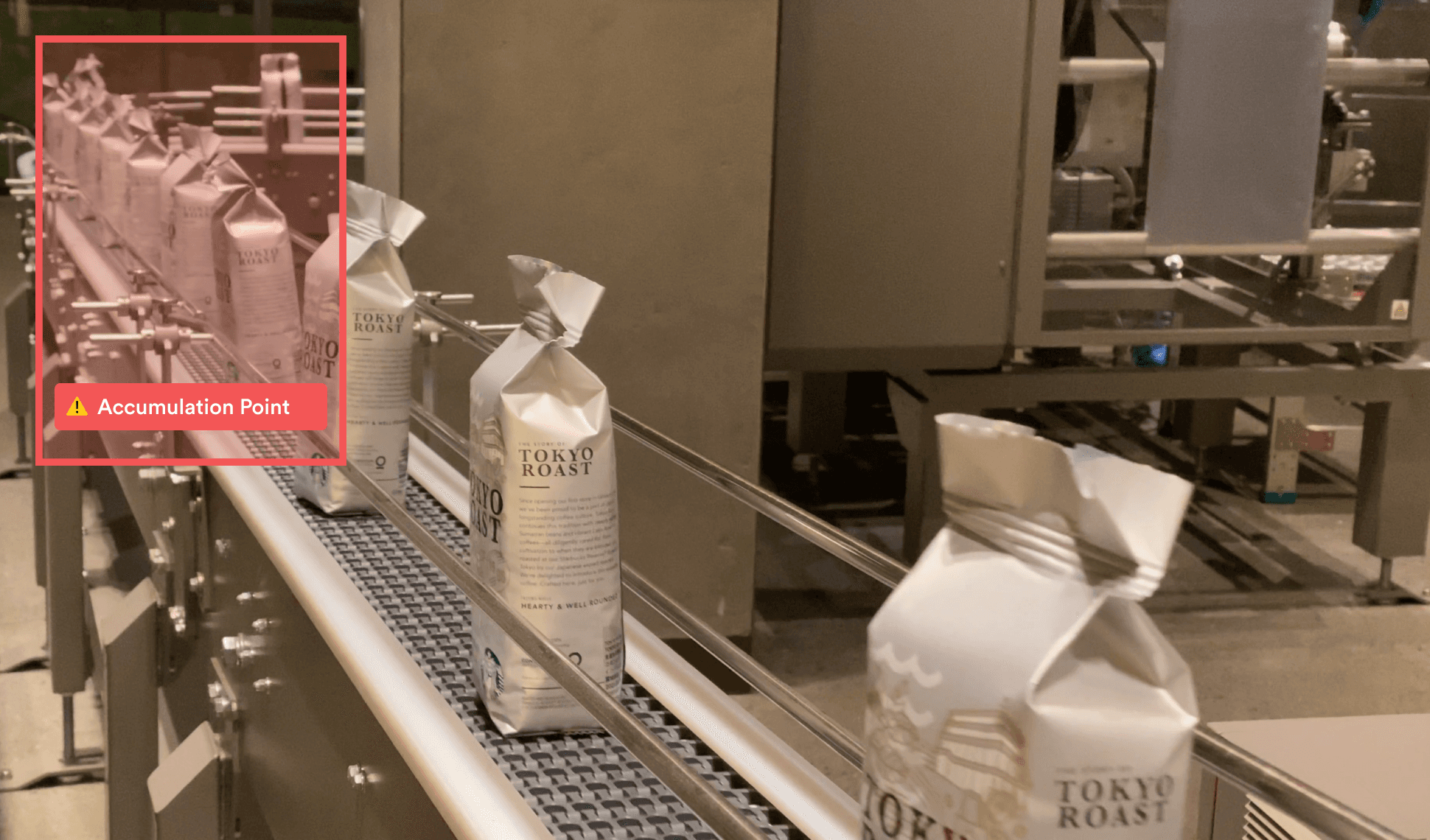
Also, Object detection, one of computer vision techniques, also involves sorting and counting and can be of great value when visually inspecting manufacturing processes. This functionality has a significant impact in the pharmaceutical industry in particular, where an incomplete blister pack or any variability in the final product could lead to severe consequences for clients. Manufacturers could also face additional legal costs if defective product liability lawsuits occur.
To reduce costs of scraps, manufacturers that carry out precise laser or rotary die-cutting of designs can also benefit from Ccomputer Vision. The models are fed images or videos with parameters as gold standards to consistently guide physical equipment, reducing variability and cost of scraps.
Safety & compliance
The physical integrity of workers should be a priority for every company, regardless of the nature of the tasks. In the manufacturing industry, there is no margin for error when it comes to the safety of human capital.
As such, manufacturers must keep track of compliance with the protocols established to ensure the safety of workers. Monitoring of accident-prone areas, emergency exits that should not be obstructed, and areas that must remain empty to allow traffic is also required.

Usually, this involves a worker overseeing several cameras facing different working stations, with workers and heavy machinery traffic. Naturally, a human cannot be constantly alert and repeatedly handle many signals without making mistakes.
Workers in this industry could risk injury when doing manual check-ups or maintenance work and walking through hazardous zones in manufacturing plants or warehouses. Sometimes, willingly or not, workers fail to follow the rules regarding safety standards and the use of personal protective equipment (PPE) like helmets, masks, or safety glasses. This not only puts the worker at risk but could also be a matter of public health in facilities that produce food products or require a sterile environment.
When human monitoring of compliance fails, the well-being of workers is compromised, and companies could face financial penalties for not abiding by the corresponding regulations. In this context, computer-vision-powered monitoring of plant conditions is an excellent solution for manufacturers. It enables a non-interrupted control of the use of PPE and remote checks in a manufacturing plant without the need for the physical presence of a worker, and with the accuracy only software can achieve.
Logistics & Inventory
The processes that involve raw material acquisition up to the distribution of the final product are no exception to the scope of the application of Computer Vision in manufacturing. Logistics are paramount to reduce lead times and fulfill internal and external clients' needs. There are also many decisions regarding storage space and transportation routes to avoid incurring additional costs and delays in the healthy flow of products.
Manufacturers can design and establish procedures for organizing inventory to feed and train computer vision models to achieve vision-based inventory control. Once in production, the models can free workers from these tedious, error-prone repetitive tasks and outperform them.
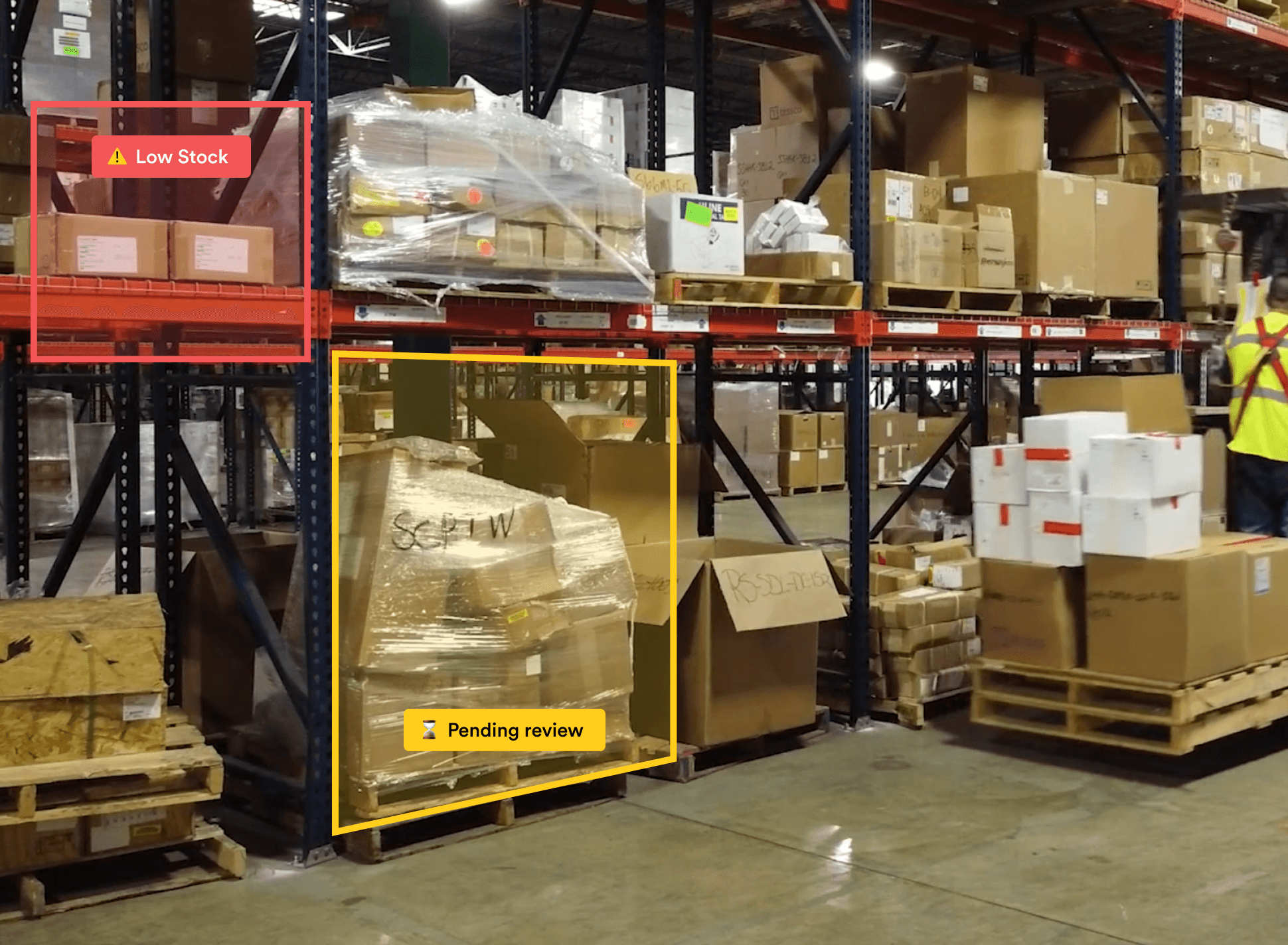
Customized computer vision algorithms embedded in the manufacturer's inventory management system aids in pinpointing the exact location of items. When cameras read a label, QR code, or a traditional barcode, the system can unmistakably identify, track and trace an object. When packages are classified and transported by their size or weight, the system emits an alert if an error is made, and workers can reroute the package.
For an optimized flux of goods, video analytics lets warehouse managers establish a beneficial distribution of the available physical space. With the added value of documenting warehouse operations, algorithms can also monitor the occupancy of traffic and storage areas to detect and recognize bottlenecks.
Computer vision-powered cameras also monitor parking lots and dock occupancy. This is extremely useful to avoid delays and increased operating costs when coordinating loading and transport of deliverables.
Closing up
We went over the main areas where Computer Vision in manufacturing adds great value in the manufacturing industry. Of course, this requires investing in good quality costs and knowing manufacturing processes in full to be able to recognize opportunities for improvement.
By now, it's clear that the ROI of predictive maintenance, catching defects early, automating inspection, and optimizing logistics far outweigh the effort required.
Additionally, manufacturers have to get their message across to computer vision specialists for a successful implementation, which can be challenging.
At Pento, we have the privilege to have team members from different backgrounds, including Process and Industrial Engineers. They combine their computer vision skills to merge both worlds to craft tailored solutions for the needs of a manufacturer client.
Are you looking for computer vision solutions for your manufacturing business? Contact us to bring you a step closer to your goals and become a Lighthouse of the industry.
stay in the loop
Subscribe for more inspiration.
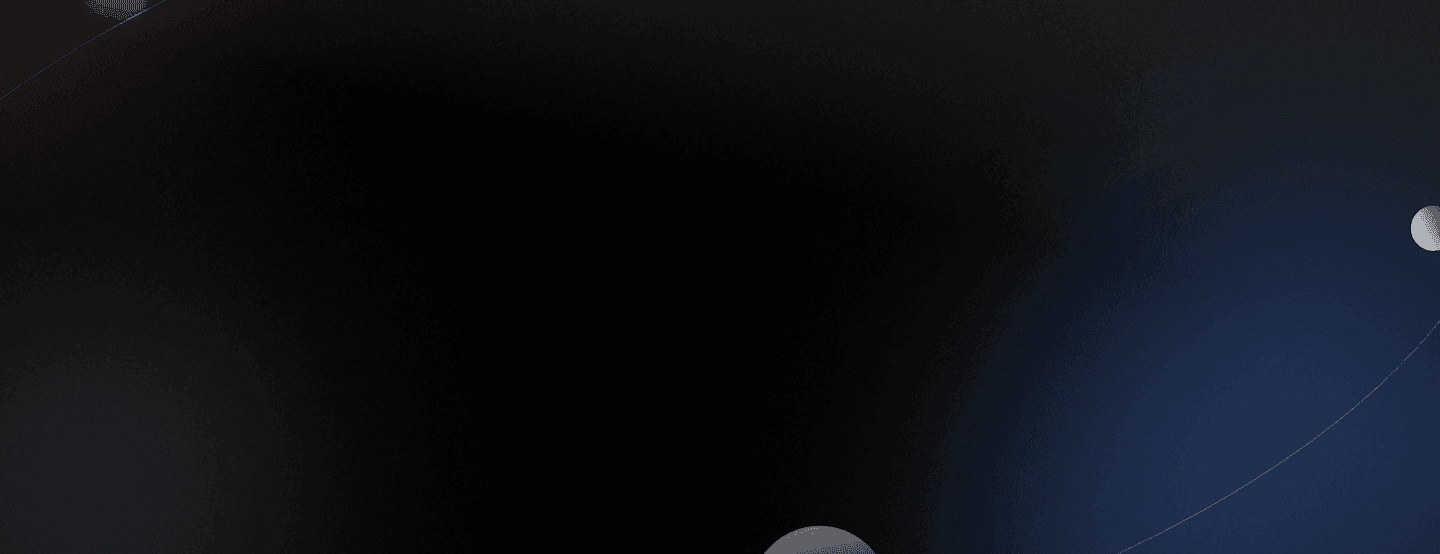